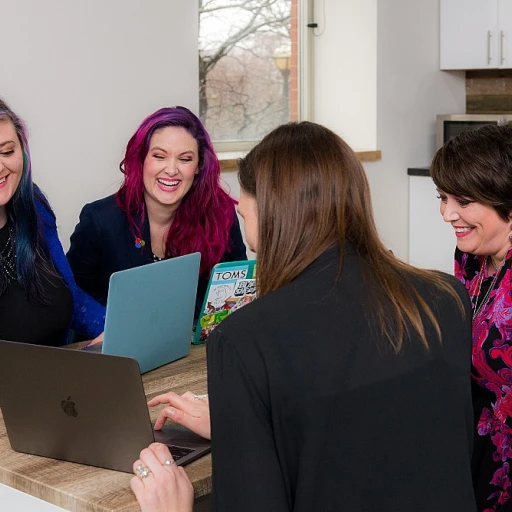
Understanding the Sales to Prefabrication Transition
{"Bridging Sales and Prefabrication in Construction
In the world of construction, the transition from sales to prefabrication marks a pivotal point in effectively managing projects. This shift involves transforming initial sales promises into concrete plans and tangible outcomes on the building site. Understanding this important phase is crucial for Indian companies aiming to optimize their construction process and leverage the benefits of modular and prefab construction. The prefabrication method involves assembling building components offsite before integrating them into the construction site. This approach can significantly reduce time, improve quality control, and lower costs when compared to traditional construction practices. However, a seamless transition requires clear communication and detailed planning from the outset. Sales teams must first align with design professionals to ensure that client expectations are feasible within the prefab construction framework. This involves:- Identifying appropriate materials and prefabricated components that meet client specifications and regulatory standards.
- Understanding the essence of modular building design and its impact on site preparation and construction methods.
- Anticipating potential challenges in transporting and assembling components manufactured offsite.
Challenges in Prefabrication for Indian Companies
Overcoming Prefabrication Hurdles in India
The transition from traditional construction to prefabrication in India presents unique challenges. While the promise of prefabrication offers efficiency and cost-effectiveness, Indian companies face several hurdles in adopting these modern construction methods.
Quality Control and Standards
One of the primary challenges is maintaining quality control. Prefabricated components must meet stringent standards to ensure they are fit for purpose. The Indian construction industry often grapples with inconsistencies in quality due to variations in materials and manufacturing processes. Ensuring that components manufactured offsite meet the required standards is crucial for the success of prefab construction projects.
Logistics and Site Preparation
Logistics also pose significant challenges. Transporting prefabricated components to the construction site requires careful planning and coordination. Site preparation must be precise to accommodate modular buildings and prefab homes. Any misalignment can lead to delays and increased costs, undermining the benefits of modular construction.
Cost Implications
Cost is another critical factor. While prefabrication can reduce time and labor costs, the initial investment in design and manufacturing facilities can be high. Companies must weigh these costs against the long-term benefits of reduced construction time and improved efficiency.
Adapting to New Processes
Finally, adapting to new construction processes can be daunting. Prefabricated construction requires a shift in mindset from traditional site construction. Training and upskilling the workforce to handle modular construction techniques is essential. This transition is not just about adopting new technologies but also about embracing a new way of working.
For more insights on overcoming these challenges, consider exploring innovative requisition solutions that can streamline procurement and enhance efficiency in prefabrication projects.
Role of Office Managers in Streamlining Processes
Enhancing Operational Flow Through Strategic Office Management
In the Indian construction industry, office managers play a pivotal role in ensuring a seamless transition from traditional site construction to efficient prefabrication processes. Their ability to oversee and streamline the workflow is crucial to capitalizing on the potential benefits prefabrication offers. Office managers are responsible for coordinating between different departments to ensure smooth communication and execution. This includes organizing and scheduling meetings between the design teams and those involved in the manufacturing of prefabricated components. By fostering an open line of communication, they help prevent potential bottlenecks in the construction process. Moreover, integrating modular construction and prefab solutions into the work culture requires effective quality control measures. Office managers need to implement meticulous quality assurance protocols to guarantee that prefabricated components meet the industry standards before they reach the construction site. A significant part of their role also involves budgeting and cost management. Given that modular buildings and prefab homes can initially seem cost-intensive, office managers must strategically allocate resources to realize longer-term savings and project optimization. Furthermore, they must ensure all team members are on board with the new processes and fully trained in offsite construction methods. This is where their skill in managing human resources comes into play, enhancing both efficiency and worker engagement. More insights on engaging employees effectively can be found in this strategic insights guide for the Indian office manager. Ultimately, office managers act as the fulcrum balancing traditional construction methods with innovative, prefabricated construction techniques. As the construction industry continues to evolve, their role in shaping its future becomes increasingly indispensable.Technological Solutions for Improved Efficiency
Leveraging Cutting-Edge Technology to Boost Efficiency
Indian construction companies, particularly in the realm of prefabrication and modular construction, are increasingly turning to technological advancements to enhance efficiency and precision in their work. The use of technology is propelling the construction industry into a new era where quality, speed, and cost-effectiveness are not mutually exclusive. Several technologies are being tailored for seamless integration into the prefabrication process:- Building Information Modeling (BIM): This digital representation of the physical and functional characteristics of a building allows for detailed planning and visualization. BIM supports the accurate design of prefab components, enabling efficient collaboration across design, site preparation, and site construction stages.
- 3D Printing: An innovative solution for manufacturing construction components, 3D printing is gradually finding its place in Indian sites. It offers the precision required for modular constructions and prefabricated components, thereby reducing waste and speeding up the construction process.
- Offsite Construction Technologies: Techniques such as computer-aided manufacturing (CAM) and automated quality control systems can produce building components in controlled environments, ensuring high quality even before the components reach the construction site. Offsite preparation is gradually complementing traditional construction methods, helping reduce project timelines.
Case Studies of Successful Implementations
Showcasing Real Success
In the evolving landscape of Indian construction, learning from successful implementations in prefabricated construction provides invaluable insights. A notable example is the construction of modular buildings in urban areas where space constraints posed significant challenges. By utilizing offsite construction methods and prefabricated components, companies were able to accelerate the construction process significantly.
One particular project highlighted the use of prefab components manufactured with high-quality materials, ensuring both durability and sustainability. This approach not only reduced the overall construction time but also minimized cost by streamlining the construction process. Moreover, the implementation of stringent quality control measures during production facilitated seamless site preparation and swift assembly onsite, a testament to the efficiency of prefabricated construction.
In another successful venture, the integration of advanced design technologies allowed for the customization of modular homes to suit varying customer preferences while maintaining a high standard of quality. By adopting prefabrication, the builders were able to deliver cost-effective solutions without compromising on the aesthetic appeal or structural integrity of the buildings.
These case studies underscore the potential of modular and prefab construction to transform the traditional construction industry in India. As building components are prefabricated, the projects benefit from an accuracy and consistency that is often challenging to achieve through conventional site construction methods. This not only enhances the overall efficiency but also offers a competitive advantage in the densely populated urban centers.